What Are Holding Costs Definition How They Work and Example
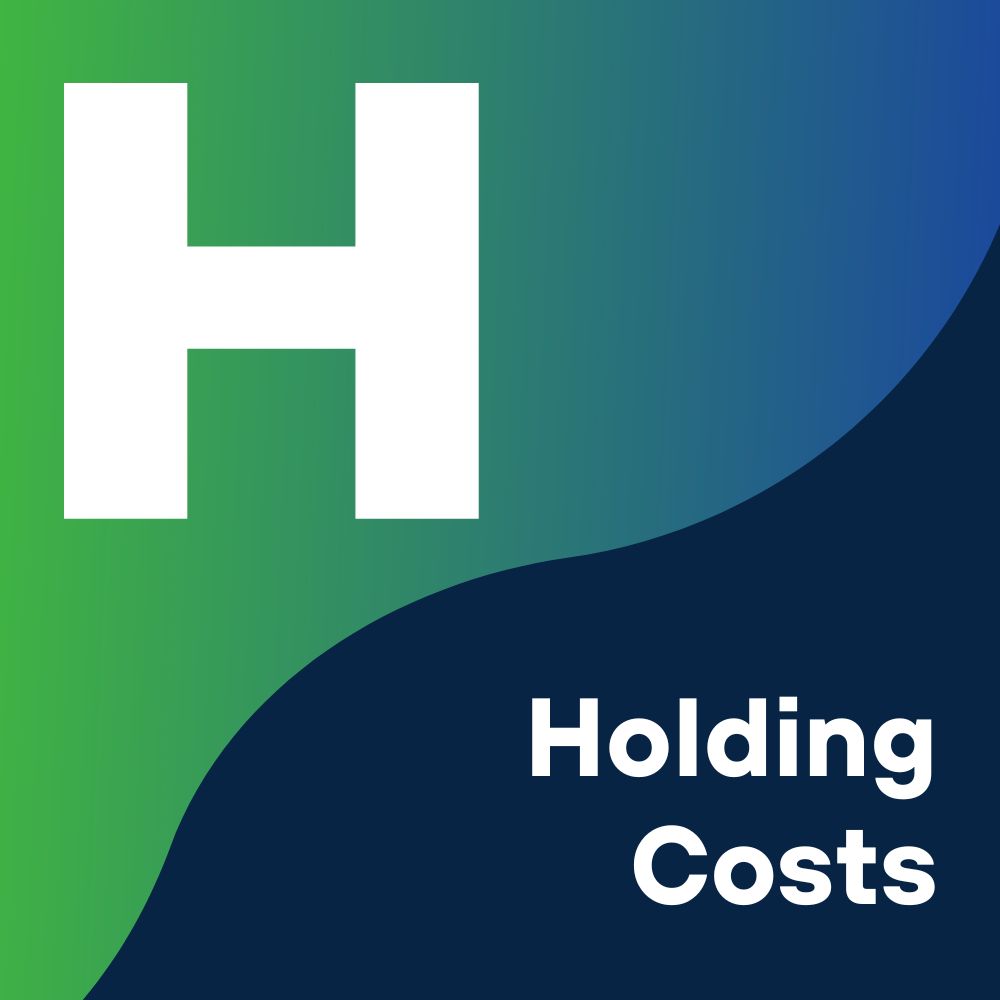
Contents
What Are Holding Costs? Definition, How They Work, and Example
What Are Holding Costs?
Holding costs are associated with storing inventory that remains unsold. These costs are one component of total inventory costs, along with ordering and shortage costs.
A firm’s holding costs include the price of goods damaged or spoiled, as well as storage space, labor, and insurance.
Key Takeaways
- Holding costs are costs associated with storing unsold inventory.
- A firm’s holding costs include storage space, labor, insurance, as well as the price of damaged or spoiled goods.
- Minimizing inventory costs is an important supply-chain management strategy.
- Strategies to avoid holding costs include quick payment collection and calculating accurate reorder points.
Understanding Holding Costs
Minimizing inventory costs is an important supply-chain management strategy. Inventory requires a large cash outlay, and decisions about inventory spending can reduce available cash for other purposes.
For example, increasing the inventory balance by $10,000 means less cash available each month. This is considered an opportunity cost.
Holding Costs Example
Assume that ABC Manufacturing produces furniture stored in a warehouse and shipped to retailers. ABC must lease or purchase warehouse space and pay for utilities, insurance, and security.
The company must also pay staff to move inventory into and out of the warehouse. The firm incurs a risk that the furniture may be damaged.
Holding Cost Reduction Methods
One way to ensure sufficient cash is to sell inventory and collect payments quickly. The sooner cash is collected, the less cash the firm needs to continue operations. Businesses measure cash collections using the inventory turnover ratio, calculated as the cost of goods sold (COGS) divided by average inventory.
For example, a company with $1 million in COGS and an inventory balance of $200,000 has a turnover ratio of five. The goal is to increase sales and reduce inventory to increase the turnover ratio.
Another strategy to minimize holding costs is calculating a reorder point. An accurate reorder point allows the firm to fill customer orders without overspending on inventory. Companies that use a reorder point avoid shortage costs, the risk of losing a customer order due to low inventory levels.
The reorder point considers the time to receive an order from a supplier and the level of product sales. It also helps compute the economic order quantity (EOQ), the ideal amount of inventory to order. EOQ can be calculated using inventory software.
The reorder point considers the time to receive an order from a supplier and the level of product sales. It also helps compute the economic order quantity (EOQ), the ideal amount of inventory to order. EOQ can be calculated using inventory software.